FLiDAR
EGS AUSTRALIA AND FRAUNHOFER COLLABORATION AND JOINT VENTURE
EGS and Fraunhofer have established a collaborative agreement where EGS is the sole developer and supplier of Fraunhofer’s advanced Floating Lidar (FLiDAR) technology in the APAC region. EGS is authorized to manufacture the technology in Australia, tailoring it to local conditions. EGS will handle the maintenance, deployment, and operation of the buoys, while Fraunhofer provides the technology, consultancy support, and experienced engineers for training and initial deployments. Additionally, Fraunhofer will assist with web hosting, data quality control, and data processing support, ensuring seamless integration and operation of the FLiDAR systems
IWES LIDAR BUOYS
Track Record:
• Development initiated in 2009
• First prototype tested in 2013
• Achieved OWA Stage-2 in 2016
• Utilized in research campaigns since 2015
• Utilized in commercial projects since 2017
• Over 35 research and validation projects
• Over 15 commercial projects
• Fraunhofer IWES operates 10 buoys
• License partner in Asia operates 18 buoys
• Actively involved in the standardization of floating lidar systems (OWA, IEA, IEC)
• OWA Stage-3 late 2023
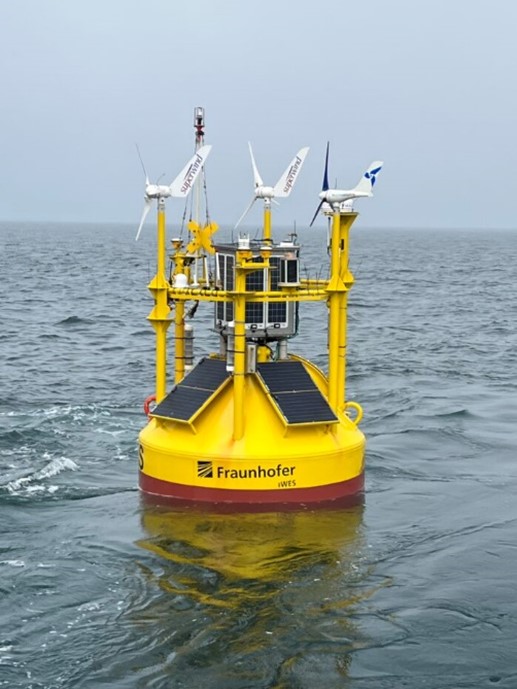
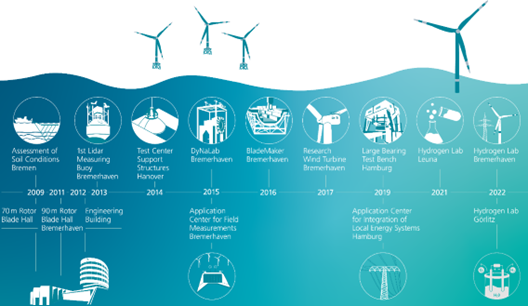
Technical Description – Buoy Specifications
4. Hull Specifications
The focus during development and production was to build a robust Floating LiDAR System (FLS) while considering the importance of power supply, data management, and redundancy. The system can withstand harsh offshore weather conditions and measure at a very high accuracy level. The IWES Wind LiDAR Buoy has safely operated during several North Sea storms and proven its performance in typhoon areas of the Pacific.
5. Technical Specifications
Dimensions: | Overall height: 9.2 m Diameter: 2.55 m Weight: 5.6 t (without anchorage) |
Operational water depth: | Minimum: 10-15 meters Maximum: 100 meters and beyond |
Material: | Steel hull: (DIN 1.0036) LiDAR housing: Anodized Aluminium Attachments: Stainless steel (DIN 1.4571) |
Colour: | RAL 1023 (standard for offshore windfarms) Additional Anti-Fouling below the water line |
Power System: | Renewable energy-based power system: PV panels (426 Wp) and micro-wind turbines (3 x 450 W). Backup energy supply: Diesel gen-set (fuel capacity up to 200l) |
Energy storage: | AGM batteries (1650Ah, 24V) ensuring power supply for up to one week |
Note: Due to different buoy versions in operation, the dimension, weight, and outfitting details might differ slightly from the final buoy chosen for the project.
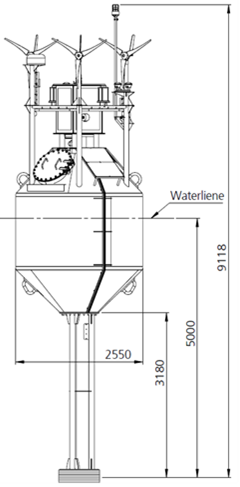
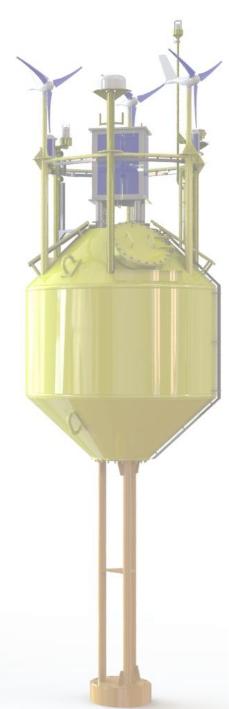
6. Corrosion Protection
To withstand the corroding effect of salty sea water the buoy is coated in the following manner:
|
Coating |
Outer Shell |
3x 200 μm 2-K-EP-Coating (Hempel HEMPADUR MULTI-STRENGTH 45751/45753) 1x 70 μm 2-K-PU-Coating (Hempel HEMPATHANE HS 55610) |
Buoy Pedestal |
3x 700 μm 2-K-EP-Coating (Hempel HEMPADUR MULTI-STRENGTH 45751/45753) |
Anti-fouling |
2x 70 μm (BASF: RELEST® Marine 522 AF Longlife) |
Inside Buoy |
1x 50 μm zinc-Coating 1x 80 μm top-coat lacquer in bright grey (SIKA-POXICOLOR SW or similar) |
Sacrificial Anodes: 6 to 10 x 2 kg (made of zinc) mounted on the base and buoy cable tray (if present)
7. Lidar Unit
ZX Lidars ZX300M
· OWA-Stage 2
· Continuous laser beam
· Range: 10 – 300 m
· 10 profiles
· Wind speed accuracy: 0.1 m/s
To withstand the offshore environment and maximize survivability, the commercial lidar unit (marine version IP68 or IP67) is fully enclosed in a sealed housing. The custom aluminum enclosure has a specially coated glass cover which allows laser light transmission. The housing also hosts a special silicon wiper, including a water sprayer system to clean the glass from any contamination. An additional cleaning jet nozzle unit, associated with a seawater pump, allows for heavy dirt cleaning.
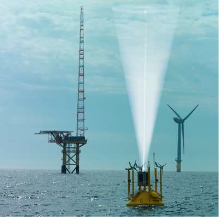
7.1 Power Supply
- Three independent sets of PV cells and micro wind turbines each linked to one battery bank
- Three independent sets of battery banks, with a total capacity for approx. one week of power supply
- One diesel generator as secondary power supply system
• Auto start or remote start via satellite communication
• Service life of up to 12 months
• Running on “environmental-friendly” GTL diesel fuel
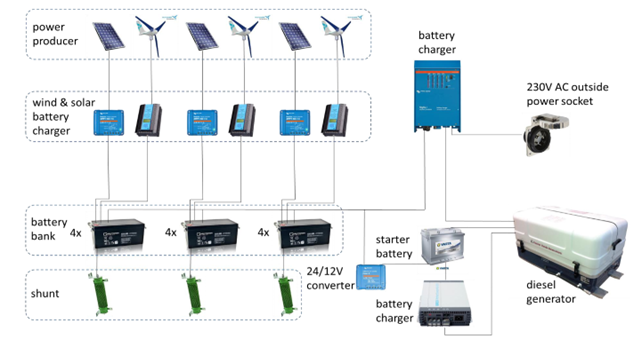
4.2 Data Transmission:
- Satellite
data uplink via Thales Iridium Certus - Iridium Short Burst (two-way communication)
4.3 Data Transmission & Analysis:
- Redundant systems ensure data security both onshore and offshore
- Verification through ICE met mast and onshore lidars
- Experienced analysts provide advanced and custom reporting
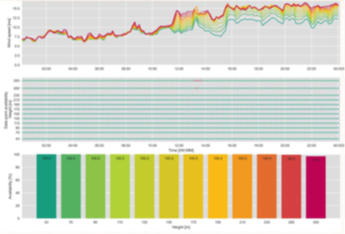
8. Navigational Marking & Aids
Based on IALA (International Association of Lighthouse
Authorities) standards and recommendations, the buoy is equipped with the
following sea marks:
- Buoy
hull and superstructure above waterline (+30 cm) colored in Traffic-Yellow
(RAL1023) - Yellow
double X mark - Radar
reflector - 2
SABIK LED Marine Lanterns (Yellow) with GPS positioning and monitoring
The flash frequency and intensity of the two SABIK LED
Marine lanterns can be individually set and the flashing is automatically
synchronized by GPS. The lanterns are autonomously powered with premium solar
components and have a rugged design. They also supply an independent position
monitoring.
The buoy can also host an AIS system, with remote switching
capability. Thus, if permitting authorities allow the usage, a license could be
obtained. Depending on the project schedule, this might be after deployment of
the buoy.
9. Navigational Marking & Aids
The IWES Wind LiDAR Buoy is equipped with two 180° IP Cameras. For power saving, both cameras are normally switched off but can be activated remotely. Footage can be retrieved through adequate GSM coverage or during buoy visits. The outer IP camera is used to check the status of the wind turbine generators and mounted equipment on the superstructure. The inner IP camera is used to visually check the buoy interior.
10. Operation and Logistics
Transportability:
· Buoy can be transported by standard truck or cargo airplane to the deployment country.
Service Concept:
· Pre-packed spare parts and tool container for repair and service jobs.
Safety Documents:
· RAMS including a vessel lifting plan and toolbox talks.
Vessel Requirements:
· Compatible with multicat vessels, experienced buoy laying vessels, and large Offshore Supply Vessels.
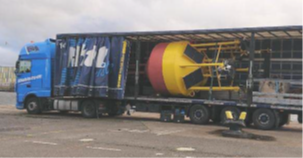
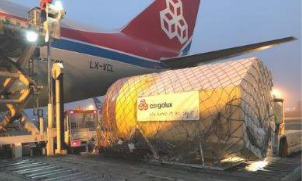
11. Validation
For the production and overhaul of the buoys Fraunhofer has a facility close to the Fraunhofer IWES headquarter in Bremerhaven. Up to now 12 units of the Fraunhofer IWES Wind LiDAR Buoy have been built with two new builds in 2023.
Further the Fraunhofer IWES Buoy is produced with alterations and operated independently from Fraunhofer IWES under a license contract by Titan Technology Cooperation in China. Up to now 15 units have been built there (Status: December 2022).
IWES Buoy Track Record
Date | Campaign* | Position | LiDAR |
Aug – Oct 2013 | Validation Campaign (BMU Research Project) | German Bight (FINO 1) | WindCube |
Aug – Sep 2014 | Validation Campaign (Test new LiDAR) | German Bight (FINO 1) | ZephIR |
Jan – Apr 2015 | Validation Campaign | German Bight (FINO 1) | WindCube |
Jun – Sep 2015 | OBLEX-F1 (Offshore Boundary Layer Exper.) | German Bight (FINO 1) | WindCube |
Jul – Sep 2015 | OBLEX-F1 | German Bight (FINO 1) | ZephIR |
Nov – Dec 2015 | RUNE (Reducing Uncertainty of Nearshore Energy) | Danish west coast | WindCube |
Feb – Apr 2016 | RUNE 2 | Danish west coast | WindCube |
Feb – Aug 2016 | ORE Catapult (stage-2 validation) | German Bight (FINO 1) | ZephIR |
Dec 2016 – Jun 2017 | DNV GL (stage-2 validation) | German Bight (FINO 3) | Windcube |
Mar 2017 – Apr 2021 | Confidential 1 (commercial project) | Scottish East coast | ZephIR/WindCube |
Dec 2017 – Apr 2019 | Confidential 2 (commercial project) | Scottish East coast | WindCube |
Mar 2018 – | Titan Buoy #1 | East China Sea | ZephIR |
Mar 2018 – | Titan Buoy #2 | East China Sea | ZephIR |
Aug 2018 – Oct 2018 | LeikLine Phase I (Power curve verification) | Irish Sea | ZephIR |
Feb 2019 – Jun 2019 | LeikLine Phase II (Power curve verification) | Irish Sea | ZephIR |
Oct 2019 – Apr 2021 | Confidential 3 (commercial project) | Scottish east cost | ZephIR |
Nov 2019 – Feb 2020 | MoBo (Ocean Monitoring) | German Bight (FINO 3) | ZephIR |
Jan – Apr 2020 | OptiDesign (Load measurement, incl. AWAC) | German Bight | ZephIR |
May 2020 – May 2021 | BSH N-6.6 & N-7.2 (commercial project) | German Bight | ZephIR |
Sep 2021 – Feb 2023 | X-Wakes/GloBE (Global Blockage Effect) | Kaskasi Gap | ZephIR |
Oct 2021 – Feb 2023 | Confidential 4 (commercial project) | Scottish East coast | WindCube |
Nov 2021 – Feb 2023 | Confidential 5 (commercial project) | Scottish East coast | WindCube |
Mar 2022 – Mar 2023 | BSH N-9 Pos.1 (commercial project) | German Bight | ZephIR |
Mar 2022 – Jun 2023 | BSH N-9 Pos. 2 (commercial project) | German Bight | ZephIR |
Sep 2023 (planned) | BSH N-13 Pos.1 (commercial project) | German Bight | ZephIR |
Sep 2023 (planned) | BSH N-13 Pos. 2 (commercial project) | German Bight | WindCube |
Oct 2023 (planned) | BSH N- 21 Pos.1 (commercial project) | German Bight | ZephIR |
Oct 2023 (planned) | BSH N-21 Pos. 2 (commercial project) | German Bight | WindCube |
* pre- and post-deployment verification measurements not included in the list
Please note: Availability figures for the campaigns can be presented upon request for some of the projects.
However, because of an increasing acceptance for floating LiDAR measurements in the offshore wind industry the number of commercially driven projects is steadily increasing.
The deployments are supervised by EGS staff and deployment and recover methods are written by EGS with the support of the vessel suppliers. The 6 monthly service visits or in between trouble shooting is performed by the same technicians and engineers who develop and build the EGS / Fraunhofer IWES Wind LiDAR Buoy. The knowledge gained by the combined service and production team is constantly used to improve the buoys and retrofits are being implemented in all units.
Due to the in-house competence usually the wind data is not only recorded and processed but also analysed by EGS for the customers. Additional service and expertise for wind measurements and modelling as well as assessment of soil conditions can be offered by EGS for the site assessment of offshore wind farms.